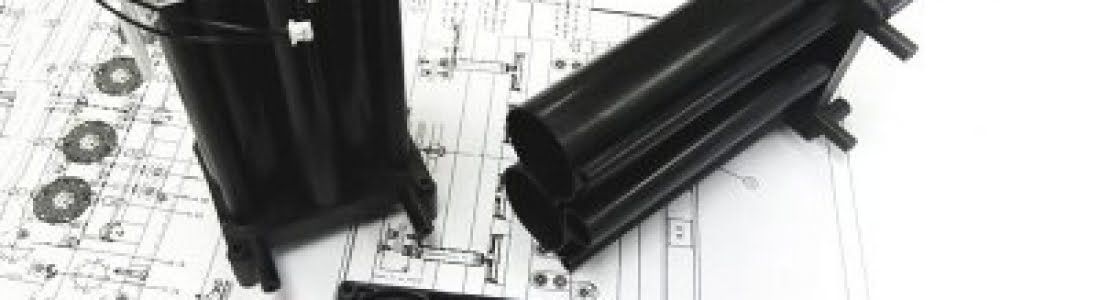
Creating Next-Generation Medical Devices And Instruments
At Precision Group, we are constantly meeting industry needs, supporting the automotive, aviation, medical, computer, electronic, oil & gas, aerospace, and consumer goods industries. On a daily basis, our team delivers molding and tooling solutions using high-tech software, equipment, and critical thinking.
In recent years, we have had the privilege of playing an important role in creating the components and parts for next-generation medical devices and instruments. Often when companies come to us for help they are under tight deadlines for product completion and are needing assistance with finding the right tooling solution to make their products work. Our clients count on us to provide sophisticated design, precision tooling, one-of-a-kind component creation, and rapid injection molding production.
Advanced Pharmacy, Alcon Surgical Inc., and Acelity are just a few of the companies we support. Kinetic Concepts, Inc. (KCI), a division of Acelity, came to us in January of 2017 with a unique challenge in the development of one of their more complex wound therapy Vacuum Assisted Closure (V.A.C) products – the V.A.C. Rx4™.
Our client was given the task, by the military, to design and develop a prototype of a multichannel negative pressure wound therapy (NPWT) device that would enable the treatment of up to four wounds on a soldier. The objective was to reduce the size and weight of the device, make it portable, compatible with other KCI disposable wound canisters, and include four independently controlled NPWT channels.
Before the Rx4 even arrived at Precision Group, several years of design, testing, and user need considerations had already been dedicated to the advanced, wound treating device.
On our customer’s side, the original scope of their project was to include a four-channel device with 300-cc canisters, simple interfaces, and no display screens. After Acelity received feedback from future users, the design changed to include a more intricate assembly that would provide 500-cc (or 1000-cc) canisters and full-color display screens.
Precision Group’s Vice President of Operations, Domingo Auces, admits this project put his team to the test. He said, “The biggest challenge was that our customer needed a water-tight seal inside a unit that contained a lot of electronics and it was made of two different types of materials. We were working with a hard plastic and a softer, more elastic plastic within the same device. To manufacture something that is made of different polymers, is not an easy task.”
Acelity brought us a pre-production prototype that had already been developed in partnership with the US Air Force Air Mobility Command and Air Combat Command. Our job was to make it functional and reproducible. We had to find a way to successfully produce and assemble the high-tech wound treatment device which included three different types of printed wiring assemblies located in separate places inside the casing. Also, the power supply location, LCD display, battery pack placement, and the front membrane panels had to be considered when planning for final assembly.
Auces emphasized, “In the end, it was determined the Rx4™ would be produced in multiple pieces involving separate molding process runs. We had to design and build the tooling required to combine both processes in injection molding – not many companies have that expertise. Our approach to solve the problem was unorthodox and that’s what allowed us to get the job done.”
The V.A.C. Rx4™ is designed to be used in the battlefield, often administered to soldiers while in motion on a fixed-wing or rotary-winged aircraft in route to definitive care. These scenarios leave zero margin for error. There can be no leaks within this device as lives are at stake. This limb saving unit, used in trauma conditions, had to be durable, and easily grabbed from the front or the side, so it could be quickly thrown onto a plane or Humvee at a moment’s notice.
The Precision Group team worked diligently for 11 and a half months to bring the multichannel device over the finish line with final adjustments and improvements that allowed the mass production of a unit that would function reliably and consistently in moments of critical need.
Auces said clear and constant communication was the key to the success of this high-profile project. “There was a lot of collaboration between our tooling manufacturing and the engineering teams from both Precision and Acelity, as well as their research and development people. The value we bring is concurrent engineering which is the continual refinement of the products we manufacture. We are constantly adapting quickly and creatively until we get to the final solution.”
There is a growing trend among medical device companies requesting design and product improvements in numerous areas of medicine. We’re here to help design and build injection molds for the production of plastic components, help solve unique industry tooling problems, or assist with cutting costs and time to delivery. With the right design and resins many of the hurdles associated with dimensional accuracy, flatness, surface finish, and mold life can be resolved.
Today, the V.A.C. Rx4™ is saving lives and limbs in conflict situations for the military, and in the future, it will surely be used in civilian environments in medical centers and hospitals throughout the country. This advanced device can help treat multiple wounds on one person or can help upward of 4 patients at a time. Finding a way to successfully manufacture the Rx4 was truly a cause worth fighting for!